بهینه سازی انرژی در صنعت فولاد
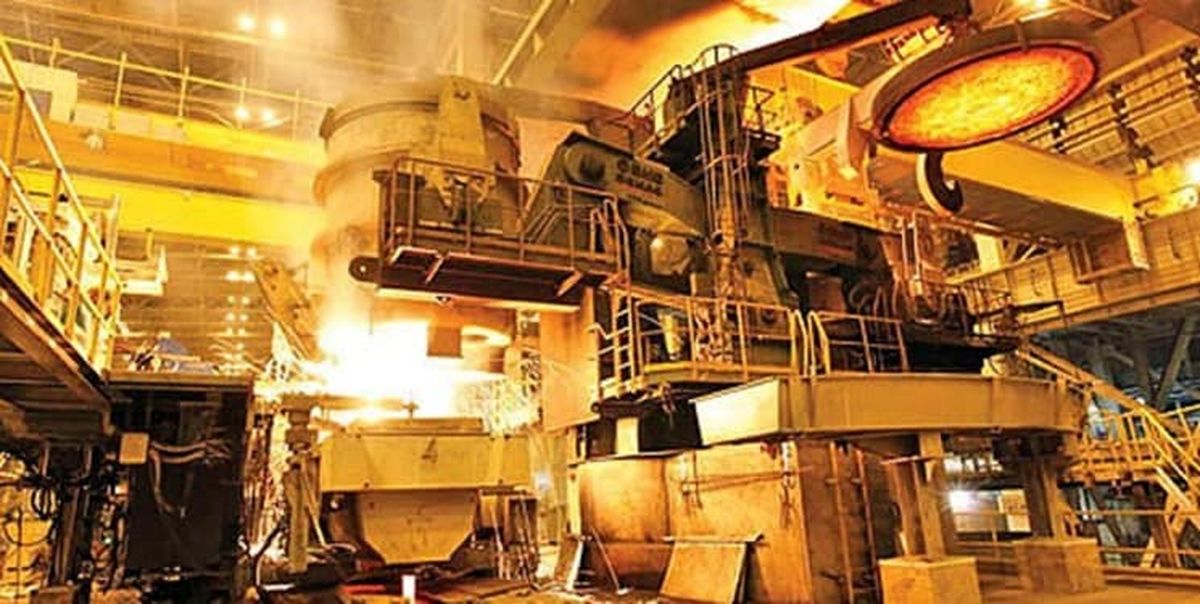
مریم رشیدخانی، مدیر مسئول سبزرسانه، دانشجوی کارشناسی ارشد مدیریت محیطزیست واحد علوم و تحقیقات تهران دانشگاه آزاد اسلامی
انسان از دیرباز در اندیشه استفاده مؤثر و مفید از تواناییها، امکانات و منابعی که در اختیار داشـته، بـوده اسـت. امـا در دنیـای صنعتی امروز، این امر بیشازپیش موردتوجه قرار میگیرد. محدودیت منابع سوخت فسیلی، افزایش بیرویه مصرف انـرژی و به دنبال آن، افزایش فزاینده گازهای گلخانهای و گسترش آلودگی محیطزیست سبب شده که موضوع کاهش مصرف انـرژی و بهینهسازی آن، از اولویتهای اساسی در بخش انرژی کشور قلمداد شود. بی شک، فـولاد یکـی از کالاهـای مهـم و اسـتراتژیک کشور در بخش صنعت میباشد. افزایش کارایی و بهرهوری عوامل تولید از جمله انرژی در کارخانجات فولاد را میتوان یکـی از راههای افزایش تولید و رسیدن به ظرفیت اسمی کارخانجات دانست. ازاینرو برای بهبود بهرهوری عوامل مؤثر در تولید فـولاد لازم است با بهرهگیری از شیوهها و متدهای علمی، تحقیقات کاربردی متناسب با شرایط و امکانات کشـور را اجـرا نمـوده و در برنامهریزیها و سیاستگذاریهای آتی از آنها بهره گرفت. در این پژوهش، به طور مروری راهکارهای بهینهسازی مصرف انرژی در صنعت فولاد مورد بررسی قرار گرفته است.
صنعت فولاد در واقع فراوری و تبدیل سنگآهن به فولاد است که سادهترین شکل ساخت آن آلیاژ آهن و کربن میباشد. همچنین در بعضی موارد تبدیل آهن به فولاد نیمهتمام یا تولید از طریق بازیافت ضایعات فلز به فولاد، در صنایع فولاد انجام میشود.
فولاد نیمهتمام یا semi-finished یک فولاد میانی است که برای تبدیل به کالاهای نهایی به پردازش بیشتر نیاز دارد.این صنعت یکی از صنایع ضروری برای توسعه هر جامعه است. انقلاب صنعتی اروپا در آغاز این قرن در واقع بر پایه این صنعت شکل گرفت.چرا که صنعت فولاد پایه بسیاری از صنایع است که بدون آن نمیتوان در آنها فعالیت کرد و این به اهمیت آن میافزاید.
روشهای تولید در صنعت فولاد
برای دستیابی به محصولات فولادی تمام شده در صنعت فولاد سه روش اساسی وجود دارد:
- تولید فولاد یکپارچه (integrated steel production)
- پردازش ثانویه (secondary processing)
- کاهش مستقیم (direct reduction)
۱- تولید فولاد یکپارچه
تولید یکپارچه فولاد شامل تبدیل زغال به کک در کورههای کک است.درحالیکه سنگآهن قبل از این که در کوره بلند (BF) تغذیه شود، پخته میشود. سنگ معدن در کوره بلند ذوب میشود تا فلز داغ حاوی %۴ کربن و مقادیر کمتری از عناصر آلیاژی دیگر به دست آید. بعد، فلز داغ در کوره اصلی اکسیژن (BOF) به فولاد تبدیل میشود. سپس، به طور مداوم برای بهدستآوردن محصولاتی که با نام فولاد نیمهتمام شناخته شدهاند، ریختهگری میشوند.
این محصولات به شکلهای نهایی زیر تولید و به بازار عرضه میشوند.
• میلهها
• ورق
• ریل
• تیرهای H
۲- پردازش ثانویه
فرایند ثانویه که اغلب مینی میل (Mini Meal) نامیده میشود، با ضایعات فولادی تولید میشوند. این محصولات در کوره قوس الکتریکی (EAF) ذوب شده و پس از تصفیه، به طور مداوم نورد میشوند. مینی میلها درگذشته تنها محصولات با درجه پایین تولید میکردند؛ اما اخیراً توانستهاند بخش درحالرشد بازار در صنعت فولاد را به دست آورند.
۳- کاهش مستقیم
روش جایگزین تولید فولاد، روش کاهش مستقیم است. در این روش، تولید با گلولههای سنگآهن با درجه بالا شروع میشود که با گاز طبیعی به گلولههای اسفنجی تغییر شکل میدهد. سپس، گلولههای آهن اسفنجی درون کوره قوس الکتریکی تغذیه میشوند. فولاد حاصل به طور مداوم ریخته میشود و به شکل نهایی درمیآید.
مواد اولیه و روش تولید
همانطور که گفته شد فولاد آلیاژی از آهن است که درصد پایینی (بین ۰.۰۲ تا ۲ درصد) کربن و مقادیری از عناصر دیگر با آن ترکیب شده است؛ لذا مواد اولیه تولید فولاد نیز عمدتاً سنگآهن، کنسانتره، گندله و کلوخه آهن است. کنسانتره یا خاکه آهن با آسیاب کردن سنگآهن به دست میآید. گندله و کلوخه نیز با استفاده از روشهای خاصی (مثل زینترینگ) در کارخانههای گندلهسازی تولید شده و بهعنوان مواد اولیه تولید فولاد به کارخانههای فولادسازی فروخته میشوند. لازم به ذکر است که کارخانههای تولید فولاد عمدتاً از کلوخه و گندله و یا قراضه آهن بهعنوان ماده اولیه خود استفاده میکنند.
بهطورکلی تولید فولاد عمدتاً به دو روش کوره بلند و احیای مستقیم انجام میشود …
کوره بلند
در روش کوره بلند، گندله آهن به همراه آهک و کُک (نوعی زغالسنگ) وارد کوره بلند شده و پس از ذوب شدن در دمای بسیار بالا آهن خام به دست میآید. سپس آهن خام در یک مبدل قرار گرفته و کربن اضافی و ناخالصیهای آن گرفته میشود تا فولاد خام تولید گردد. در کشور ما از این روش در شرکت ذوبآهن اصفهان استفاده میشود.
روش احیای مستقیم
روش احیای مستقیم از دو بخش تولید آهن اسفنجی و سپس ذوب آن در کورههای الکتریکی و با استفاده از جریان بسیار قوی برق تشکیل میشود. در این روش ذرات اکسیدی آهن (سنگآهن) در تماس با گازهای احیاکننده مثل هیدروژن و مونواکسید کربن در دمای ۷۵۰ تا ۹۰۰ درجه سانتیگراد احیا شده و به آهن اسفنجی تبدیل میشوند. سپس آهن اسفنجی بهدستآمده در کورههای الکتریکی بسیار بزرگی قرار گرفته و با استفاده از جریان بالای برق فرایند ذوب و فولادسازی صورت میگیرد..
از مزایای استفاده از این روش نسبت به کوره بلند عدم نیاز به زغالسنگ (کُک) بهعنوان منبع حرارت و استفاده از جریان برق، کاهش آلودگیهای زیستمحیطی و عدم نیاز به مواد اولیه فراوری شده (مثل گندله) را میتوان نام برد.
نهایتاً پس از طی مراحل فوق و با استفاده از یکی از روشهای کوره بلند یا احیای مستقیم، سنگآهن استخراج شده از معادن تبدیل به شمش فولاد خام شده و برای تولید محصولات بعدی آماده میشود.
سیاستگذاری دولت در حوزه صنعت فولاد
در سالهای گذشته صنعت فولاد بهعنوان یک صنعت استراتژیک به لحاظ تأمین نیاز داخلی و همچنین افزایش صادرات کشور موردتوجه دولتهای مختلف بوده و نقش پررنگی در برنامههای توسعه کشور داشته است. فعالان حوزه فولاد نیز همواره بر لزوم توجه دولت به این بخش اساسی تأکید داشتهاند. مواردی همچون آزادسازی قیمت در بورس کالا (که تا حدودی محقق شده است)، ایجاد مزیت در خرید حاملهای انرژی و سوخت بهعنوان ماده اولیه، تأمین منابع مالی موردنیاز برای راهاندازی طرحهای توسعه، ثبات اقتصادی و همچنین کنترل تورم میبایست در سیاستگذاری کلان اقتصاد در نظر گرفته شود.
یکی از مهمترین مواردی که میتواند هزینه شرکتها را کاهش دهد، مجاورت واحدهای فولادسازی با دریا است. در صورت نزدیک بودن به دریا دیگر شرکتها مجبور نیستند هزینه زیادی بابت حملونقل متحمل شوند. با کاهش هزینههای مربوط با حملونقل، هزینههای تولید این محصول نیز به میزان قابلتوجهی کاهش پیدا میکند.
مشکلات زیستمحیطی در صنعت فولاد
تولید فولاد تأثیرات زیادی بر محیطزیست از جمله انتشار گازهای گلخانهای و ناسالم در هوا و ایجاد پسماندهای خطرناک دارد. هم چنین مشکل زبالههای جامد تولید شده از صنعت آهن و فولاد نهتنها مانع استفاده از میلیونها مترمربع زمین برای اهداف مفیدتر میشود؛ بلکه سبب آلودگی آن نیز میگردد.
بسیاری از این مواد زائد حاوی فلزات سنگین مانند باریم، تیتانیوم و سرب هستند. خطرناک بودن سلامت فلزات سنگین و مواد سمی کاملاً شناخته شده است. همه این مسائل باعث درنظرگرفتن قوانین سرسختانه در کشورهای حامی محیطزیست مانند کشورهای عضو اتحادیه اروپا شده است.
موارد زیر بخشی از مسائل پیش رو در صنعت فولاد هستند.
۱- تغییرات اقلیمی
تقریباً تمام انتشارات گازهای گلخانهای مرتبط با تولید فولاد از انتشار دیاکسیدکربن مربوط به مصرف انرژی در این شرکتها است.
۲- آلودگی هوا
تولید کک یکی از بزرگترین منابع اصلی آلودگی تولید فولاد است. گازهایی مانند گاز کک، نفتالین، ترکیبات آمونیوم، روغن سبک خام، گوگرد و گردوغبار کک از کورههای کک آزاد میشوند که سبب آلودگی هوا میشود.
۳- آلودگی از طریق انتشار در آب
از آب برای خنککردن کک پس از پایان پخت استفاده میشود. این آب به کک و سایر ترکیبات آلوده میشود و این در حالی است که حجم آب آلوده میتواند زیاد باشد. بهعلاوه، آبهای زیرزمینی به دلیل رسوب احتمالی این مواد زائد مستعد ابتلا به مشکلات جدی آلودگی هستند.
آسیبهای محیطی کارخانههای صنعت فلزات
این کارخانهها علاوه بر اثرات مثبتی که بر اقتصاد کشور دارند، اما آسیبهای زیستمحیطی فراوانی نیز با خود به همراه دارند.
این کارخانهها از بزرگترین منابع آلودهکننده محیط هستند که سالانه مقدار زیادی گاز کربندیاکسید را وارد محیط میکنند. حتی روشهای تولیدی متفاوتی که کارخانهها به کار میبرند، میزان آلودگی متفاوتی تولید میکند. برای مثال استفاده از کوره بلند نسبت به روش احیای مستقیم، کربندیاکسید بیشتری تولید میکند.
از دیگر معایب این کارخانهها مصرف بالای انرژی است. برای مثال در برخی از روشهای تولید فولاد از کک استفاده میشود؛ اما در برخی روشها از گاز طبیعی. حتی کیفیت مواد اولیه مورداستفاده، نوع فولادی که قصد تولید آن را داریم و حتی فناوریهایی که شرکتها استفاده میکنند نیز بر میزان آلایندهها تأثیر مستقیم دارد.
در بخش قبل گفتیم که نزدیکی به دریا میتواند منجر به کاهش بهای تمامشده کالای تولید شده بشود. اما شرکتهای مجاور دریا از آب آن بهمنظور خنککردن تجهیزات، کورهها، محصولات و… استفاده میکنند. اما این نزدیک بودن کارخانهها به دریا و استفاده از آب دریا بهمنظور خنککردن باعث آلودهشدن آب دریاها میشود.
پسابهای صنعتی نیز نقش فراوانی در آلودگی منطقه دارند. علاوهبرآن CO ،NOx SOx و ذرات معلق مهمترین آلایندههای صنعت تولید آهن و فولاد هستند. همچنین با بررسی خاک مناطقی که این شرکتها در آن احداث شدهاند، آلودگیهایی نظیر فلزات سنگین مثل سرب، روی و… مشاهده میشود.
حرکت صنعت فولاد به سمت کاهش مصرف
بهطورکلی، از حدود چهار دهه قبل تاکنون، میزان مصرف انرژی بهازای هر تن فولاد بهخاطر تحقیقاتِ انجامشده و تکنولوژیهای جدیدِ بهکارگرفتهشده روند نزولی داشته و حدود ۵۰ درصد کاهشیافته است. البته میزان انرژی مصرفی در واحدهای فولادسازی به نوع روش تولید یعنی کوره بلند یا کوره قوس الکتریکی بستگی دارد. روش کوره بلند نسبت به روش قوس الکتریکی انرژی بیشتری مصرف میکند. در ایران اگرچه آمارها کمی دچار پراکندگی هستند، این اختلاف به حدود ۲۵ درصد میرسد.
از مهمترین تکنولوژیها و فرایندهای نوین در زمینه کاهش مصرف انرژی در صنعت فولاد جهان میتوان به این موارد اشاره کرد: کنترل بهینه مواد شارژ فلزی و افزودنیها، شارژ مستقیم آهن اسفنجی داغ و بریکت داغ، کنترل پارامترهای اپراتوری مانند دما، آنالیز سرباره، آنالیز فولاد خام، آنالیز آهن اسفنجی شامل کربن و درجه فلزی شدن، کنترل میزان اکسیژن در دود خروجی، بهبود کیفیت سرباره پفکی یا اسفنجی، بهینهسازی سیستم مکش دود، افزایش هرچه بیشتر سهم انرژی شیمیایی (اکسیژن، کک و گاز) بهجای انرژی الکتریکی از طریق افزودن مشعلهای جانبی کوره قوس الکتریکی، کاهش توقفات، آموزش نیروی انسانی، مدلسازی و کنترل فرایند تولید از طریق نرمافزار و شارژ شمش ریختهگری شده داغ به کوره پیشگرم نورد. همچنین در حوزه تولید آهن اسفنجی نیز روشهای جدید مانند تزریق اکسیژن و پوشش آهک تأثیرات مهمی در کاهش مصرف انرژی داشتهاند. برخی از تکنولوژیهای جدید که هنوز در حد پایلوت و یا در ابعاد کوچکتر صنعتی شروع به کارکردهاند، از جمله استفاده از کورههای ذوب دوقلو، روش جدید ذوب و احیای مستقیم، روش ذوب و ریختهگری تختال نازک، میکرومیلها (در برابر مینیمیل) و روش جدید میدا (MIDA) در نورد میلگرد نیز بهعنوان راههای کاهش بیشتر انرژی درحالتوسعه هستند.
رویکردی برای صرفهجویی
بهطورکلی، بیشترین مصرف انرژی حرارتی گاز در صنعت فولاد مربوط به واحد احیای مستقیم و بیشترین مصرف انرژی الکتریکی نیز مربوط به کوره قوس الکتریکی است. مجتمع فولاد خراسان از سال ۱۳۹۴، با تجدید ساختار در مدیریت انرژی و تشکیل شورایعالی انرژی، کمیته اجرایی انرژی و کمیتههای فرعی مدیریت انرژی در نواحی تولیدی و پشتیبانی فنی، عزم خود را برای بهینهسازی مصرف انرژی جزم کرد و در سال ۱۳۹۵، با اخذ گواهینامه استاندارد جهانی مدیریت انرژی (۵۰۰۰۱ ISO)، اولین گام را برداشت. این شرکت در سالهای ۱۳۹۶ تا ۱۳۹۸ به ترتیب به حدود ۵درصد، ۱٫۵ درصد و ۳٫۵ درصد کاهش مصرف انرژی نسبت به هرسال قبل از آن دستیافت. از طرف دیگر، برای محکزدن بیشتر عملکرد خود، با مشارکت در سه دوره جایزه ملی انرژی، به تندیسهای برنزین و سیمین دوستاره انرژی نیز دست پیدا کرد.
مروری بر بهینهسازی مصرف انرژی در صنعت فولاد
مروری بر مطالعات پیشین در خصوص بهرهوری انرژی
مطالعات مختلفی در کشورهای گوناگون و در داخل کشور انجام پذیرفته است. دشتی (۱۳۸۱) به بررسی بهرهوری انرژی در صنعت سیمان پرداخته، با استفاده از سه شاخص سولو، کندریک و ترانسلوگ، بهرهوری را مورد بررسی قرار داده و راهکارهایی در جهت افزایش بهرهوری انرژی ارائه نموده است. راهکارهای قابلاجرا در کارخانه سیمان شمال جهت بهینهسازی مصرف انرژی الکتریکی توسط ذبیحی و همکاران (۱۳۸۵)ارائه شد. شایگان و راستگفتار (۱۳۸۵) به بهبود مصرف انرژی در صنعت کاشی و سرامیک پرداختهاند. در گزارشی که توسط شرکت میدرکس ارائه شد، مصارف ویژه تولید فولاد مذاب به روش احیای سیستم، کوره بلند و سایر روشهای جایگزین مقایسه و آمار بهترین عملکرد جهانی در روشها ارائه شده است. یکی دیگر از منابع مطالعاتی در زمینه تعیین شاخصهای مصرف انرژی در صنعت فولاد، گزارشهای سازمان انرژی ایالات متحده امریکاست. در گزارش دیگری علاوه بر تاریخچه و تشریح جزئی فرایند، بهترین نمونههای عملی، پتانسیلهای صرفهجویی بر مبنای تکنولوژی موجود و تکنولوژی مدرن و نتایج پروژههای بهینهسازی مصرف انرژی انجامگرفته در امریکا مطرح شده است .
پتانسیلهای صرفهجویی انرژی در صنعت آهن و فولاد
بر اساس برآوردهای انجام شده، با تدوین استانداردهای جدید و توجه به امر صرفهجویی انرژی در این صنعت، امکان صرفهجویی انرژی تا ۴/۲۳% به مقدار ۱۰۸۴ ژول وجود دارد. همچنین با افزایش ظرفیت تولید فولاد در کشور تا ۵۵ میلیون تن در سال ۱۴۰۴، انرژی موردنیاز برای تولید فولاد به میزان ۲۱۴ % افزایش خواهد یافت. در صورت تحقق برنامههای صرفهجویی انرژی و دستیابی به استانداردهای تدوین شده، میتوان صرفهجویی بالغ بر ۱۰۲۶۴ ژول را انتظار داشت که معادل نیمی از انرژی مصرفی حال حاضر صنعت آهن و فولاد کشور است.
راهکارهای بهینهسازی مصرف انرژی در صنعت فولاد
در صنعت تولید فولاد، بالاترین میزان مصرف گاز مربوط به فرایند احیای مستقیم و بالاترین میزان مصرف برق در کوره قوس الکتریکی میباشد. روشهای بهینهسازی مصرف انرژی در واحد احیای مستقیم شامل سیستم بازیابی حرارت، تولید گاز احیایی در کوره، افزایش کربن در آهن اسفنجی، استفاده از سنگآهن کلوخه هماتیتی، افزایش دمای گاز ورودی به کوره، تزریق اکسیژن، تجهیزات پوششدهی گندله و تغذیه آهن اسفنجی داغ میباشد.
همچنین روشهای بهینهسازی مصرف انرژی در کوره قوس الکتریکی شامل متالورژی ثانویه، استفاده از کوره با توان بالا، تولید سرباره پفکی، استفاده از مشعلهای گازی، کوره پاتیلی، پیش گرمکردن قراضه، سیستم دمش گاز خنثی از کف کوره، افزایش ولتاژ ثانویه ترانسفورمر و سیستم تزریق اکسیژن به همراه کربن است.
مهمترین منبع در خصوص راهکارهای بهینهسازی مصرف انرژی در صنعت آهن و فولاد، گزارش ارائه شده توسط دانشگاه برکلی است که شامل اطلاعات بسیار مفیدی از راهکارهای اجرایی شده در این بخش از صنعت کشور امریکا میباشد.
در این گزارش، اقدامات بهرهوری انرژی شامل راهکارهایی چون آمادهسازی سنگآهن، بازیافت حرارت آکلومراسیون، کاهش نشتی هوا، افزایش عمق بستر، بهبود کنترل فرایند، استفاده از سوختهای بازیافتی در پخت، ککسازی، حرارتدهی مبتنی بر برنامه زمانی، فولادسازی، تزریق زغالسنگ ساییده تا ۱۳۰ کیلوگرم بر تن آهن، تزریق زغالسنگ ساییده تا ۲۲۵ کیلوگرم بر تن آهن، تزریق گاز تا ۱۴۰ کیلوگرم بر تن آهن، تزریق گاز کک و گاز کوره اکسیژن اولیه، بازیافت گاز کوره، خودکار نمودن کوره داغ، بهبود سیستم کنترل کوره، ریختهگری، بهبود حرارتدهی، نورد گرم، کنترل فرایند نورد گرم، کنترل سطح اکسیژن، نورد سرد، استفاده از سیستم خودکار پایش و هدفگذاری، استفاده از سیستم پایش و مدیریت انرژی، فولادسازی کوره قوس الکتریکی، استفاده از درایوهای سرعت قابل تنظیم و استفاده از مشعلهای نوع اکسیژن غنی شده است.
روشهای بهینهسازی مصرف انرژی در واحد احیای مستقیم میدرکس
۱- سیستم بازیابی حرارت – Recuperator Utilization
-۲ تولید گاز احیایی در کوره –In Situ Reforming
-۳ افزایش کربن در آهن اسفنجی
-۴ استفاده از Lump ore در بار کوره
-۵ افزایش دمای گاز ورودی کوره
-۶ تزریق اکسیژن (Oxygen Injection )
-۷ تجهیزات پوششدهی گندله (Oxide Coating)
-۸ تغذیه آهن اسفنجی داغ (Hot DRI Charging –Hot Link )
-۹ سیستم OXY+
روشهای بهینهسازی مصرف انرژی در کوره قوس الکتریکی
۱- متالورژی ثانویه (Secondary Metallurgy)
۲- کوره با توان بالا (UHP)
۳- تولید سرباره پفکی (Foamy Slag)
۴- مشعلهای گازی (Oxy Fuel Burners)
۵- بهکارگیری (Hot Heel)
۶- کوره پاتیلی (Ladle Furnace)
۷- پیش گرمکردن قراضه (Scrap Pre Heating)
۸- سیستم دمش گاز خنثی از کف کوره (EAF Bottom Stirring)
۹-افزایش ولتاژ ثانویه ترانسفورمر (High Voltage)
۱۰- سیستم تزریق اکسیژن به همراه تزریق کربن
نتیجهگیری
ازآنجاکه تصمیمگیری در خصوص ارتقای بهرهوری از مسائل مهم صنعت میباشد، ارائه راهکارهایی جهت بهینهسازی مصرف انرژی، از مسائل مهم در این راستا میباشد. صنعت فولاد بهعنوان صنعت مادر و یکی از پرمصرفترین صنایع شناخته میشود. همچنین، طبق سند چشمانداز ۲۰ساله میزان تولید فولاد در کشور رو به افزایش است.
لذا، توجه به استفاده بهینه از منابع انرژی ضروری مینماید.
منابع:
- سایت خبری پارسیان بورس
- سایت خبری نمناک
- سایت خبری فولاد خبر
- مقاله راهکارهای بهینهسازی مصرف انرژی در صنعت فولاد کشور – نویسنده: عبدالله اعزازی، مسعود عزتی، حمید زواری – سال ۱۳۸۸
- مقاله مروری بر بهینهسازی مصرف انرژی در صنعت فولاد – نویسنده: علیرضا توانا – سال ۱۳۹۷